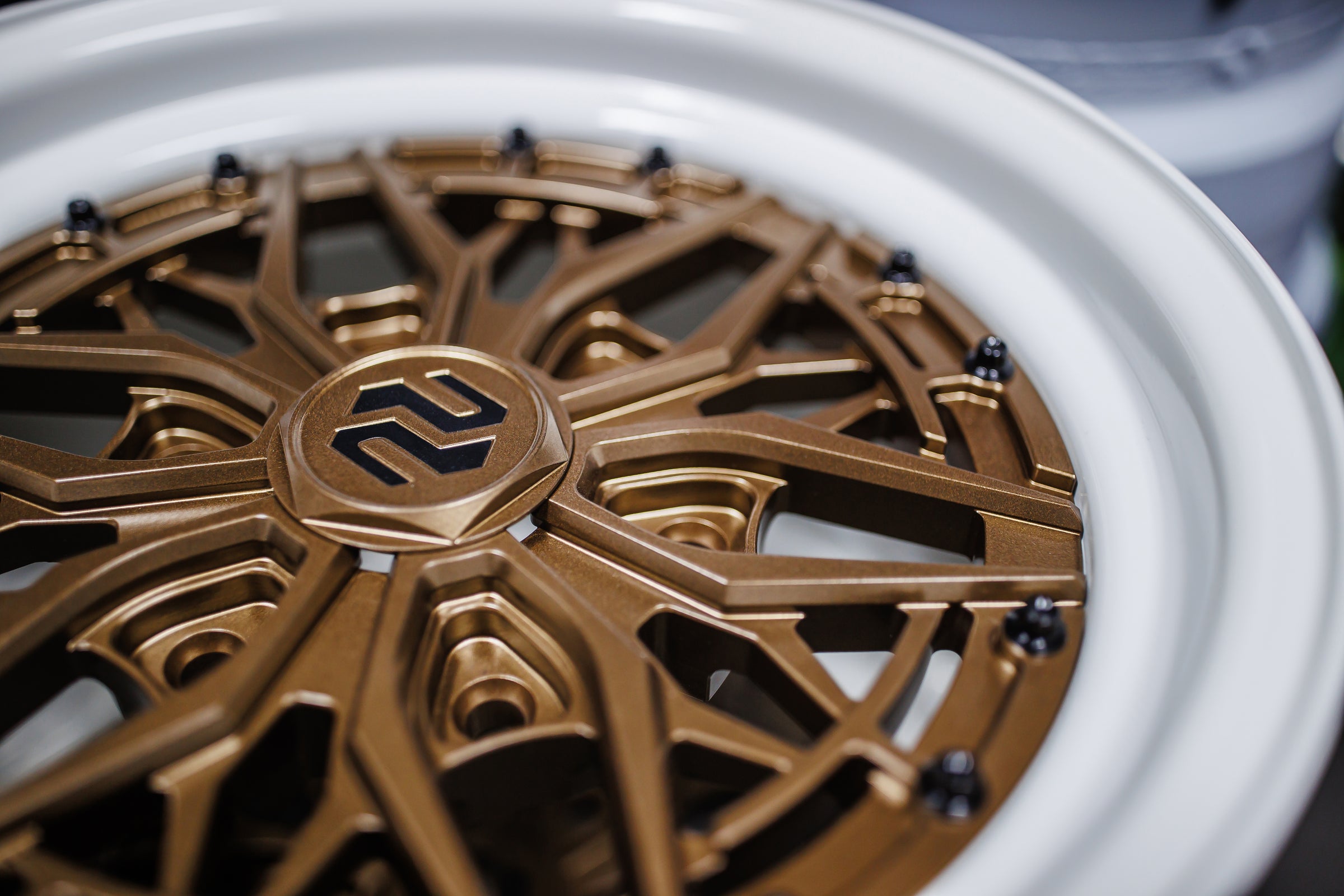
manufacturing
An inside look on the manufacturing process at Price Designs.
1. FORGING
Price Designs wheel center forgings are formed by a forging process utilizing American T6-6061 Aluminum. The forging process uses high pressure and temperature to change the non-directional grain structure of the aluminum stock material, into the high-integrity, multi-directional grain structure of forgings. The aluminum remains solid throughout the process as the forging dies come together and change the shape of the stock. The resulting directional orientation of the grain structure places the highest material strength in the same direction as the highest operating loads.
The world’s leading aircraft and aerospace manufacturers use one-piece forgings for superior performance in critical structural applications. After the desired shape, size, and profile is achieved, each forging is passed through a series of heat treatments, ensuring top-tier durability, and longevity.
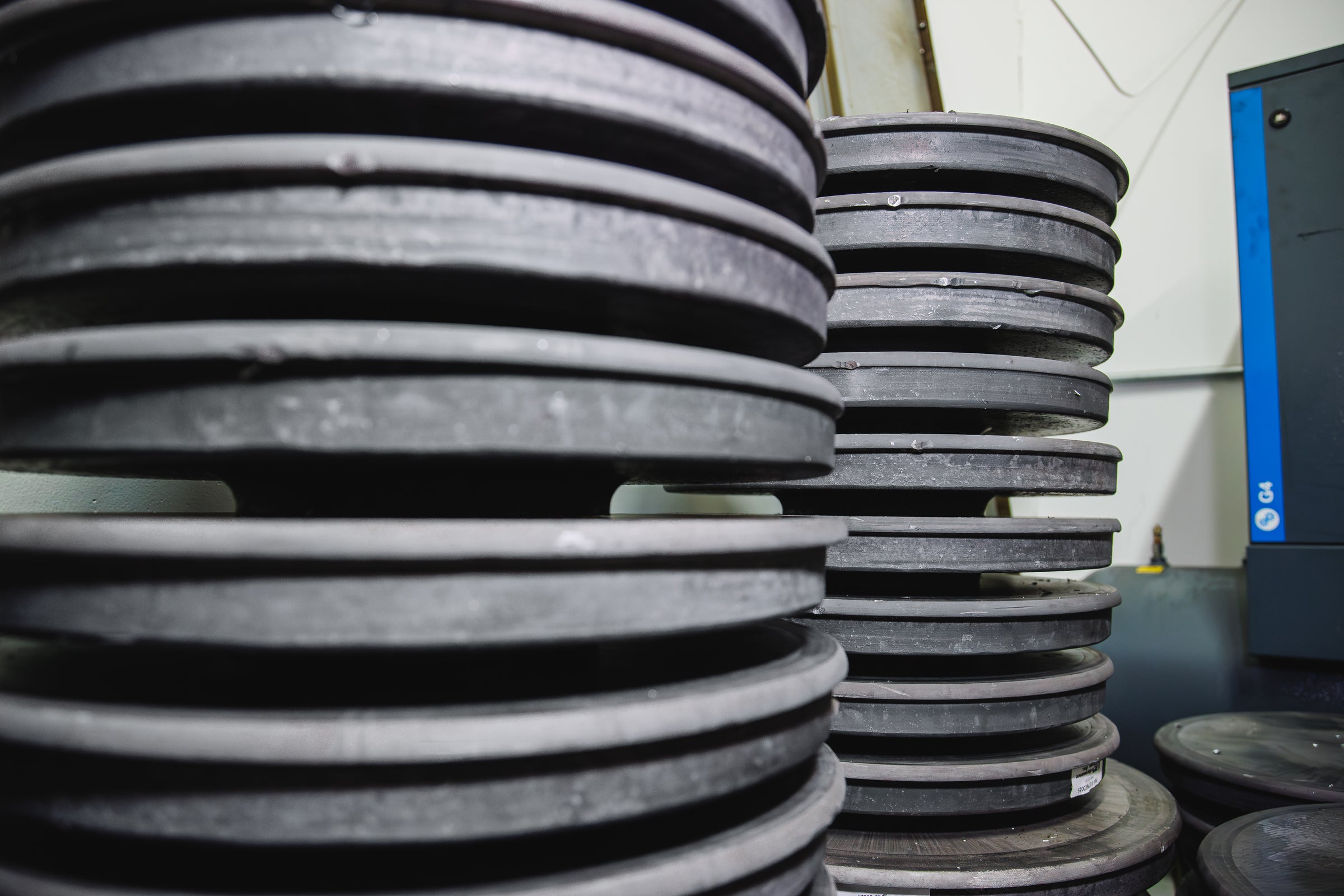
2. CNC MACHINING
CNC milling operations involve removing aluminum material from the forgings using rotary cutting tools. This allows us to achieve the finishes, shapes and contours found across Price Designs wheels. We hold +/- .001” (one thousandth of an inch) tolerances across all components manufactured in-house on both horizontal and vertical CNC mills from Haas, and Mazak.
This process of cnc milling wheel centers is precise, repeatable, and allows us to be efficient in our production of many different models, lug patterns, and diameters. Understanding this process helps the customer to appreciate the craftsmanship, design and work that’s required to produce our wheels at an efficient pace, with perfect accuracy.

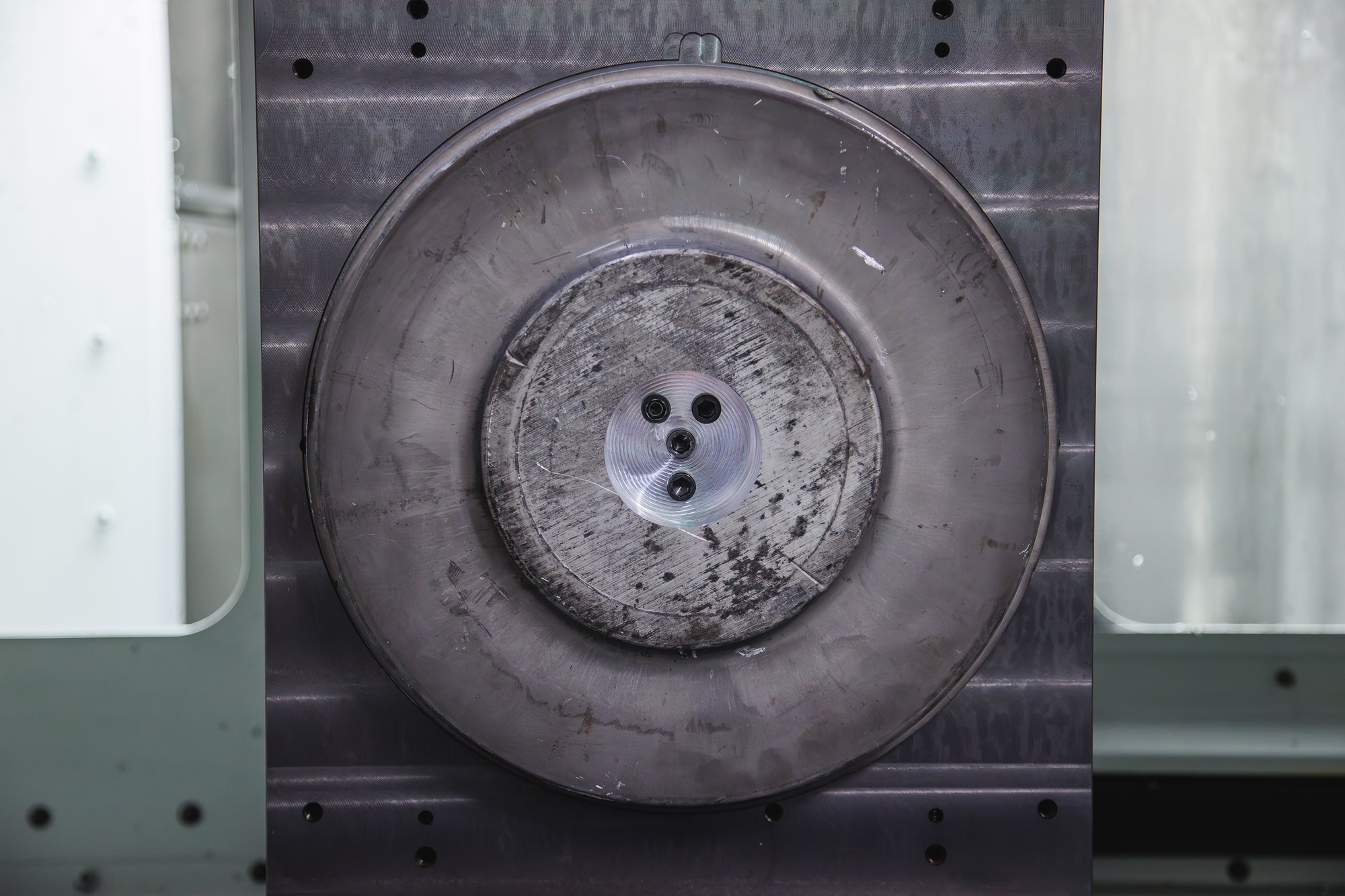
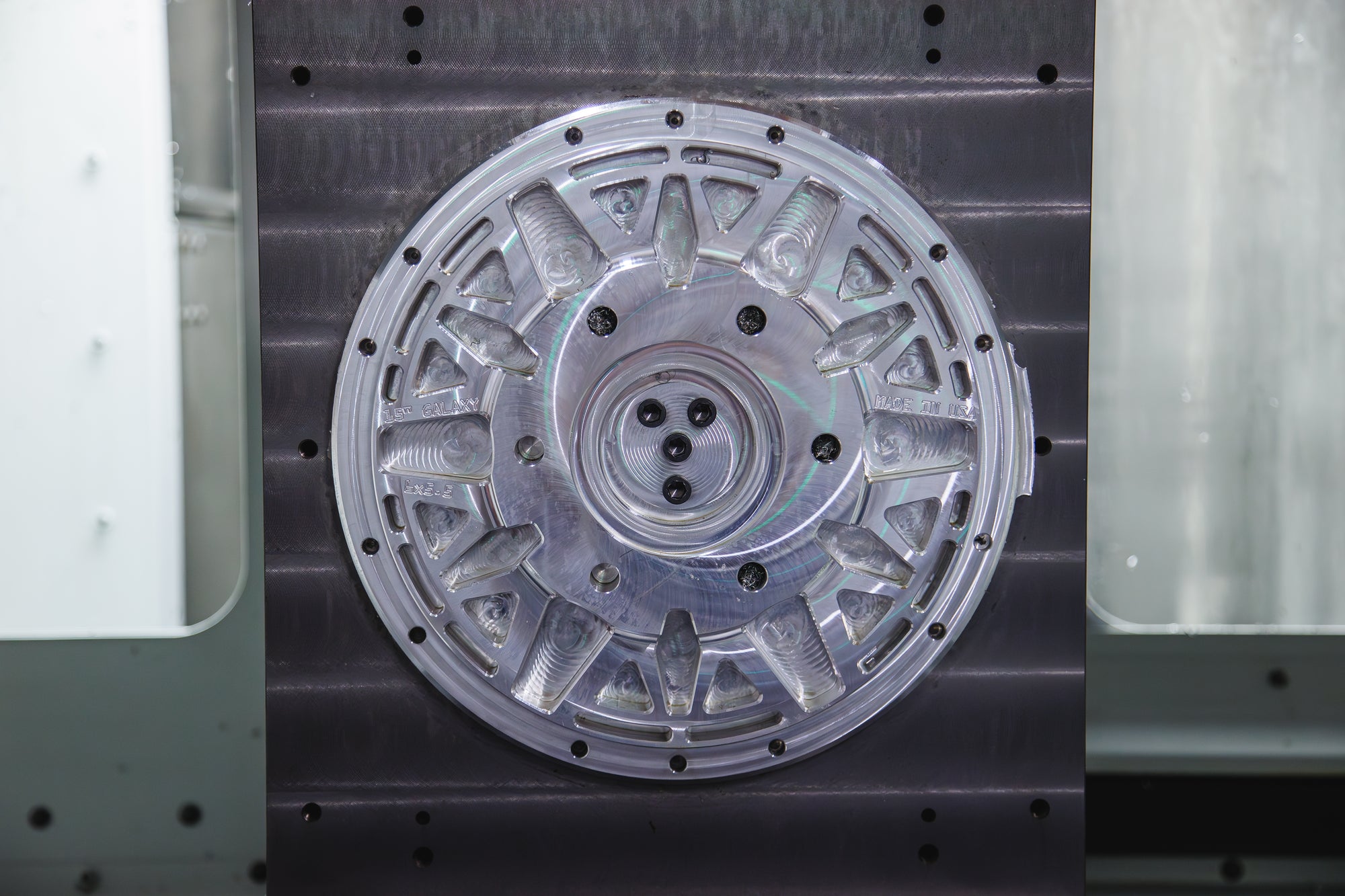
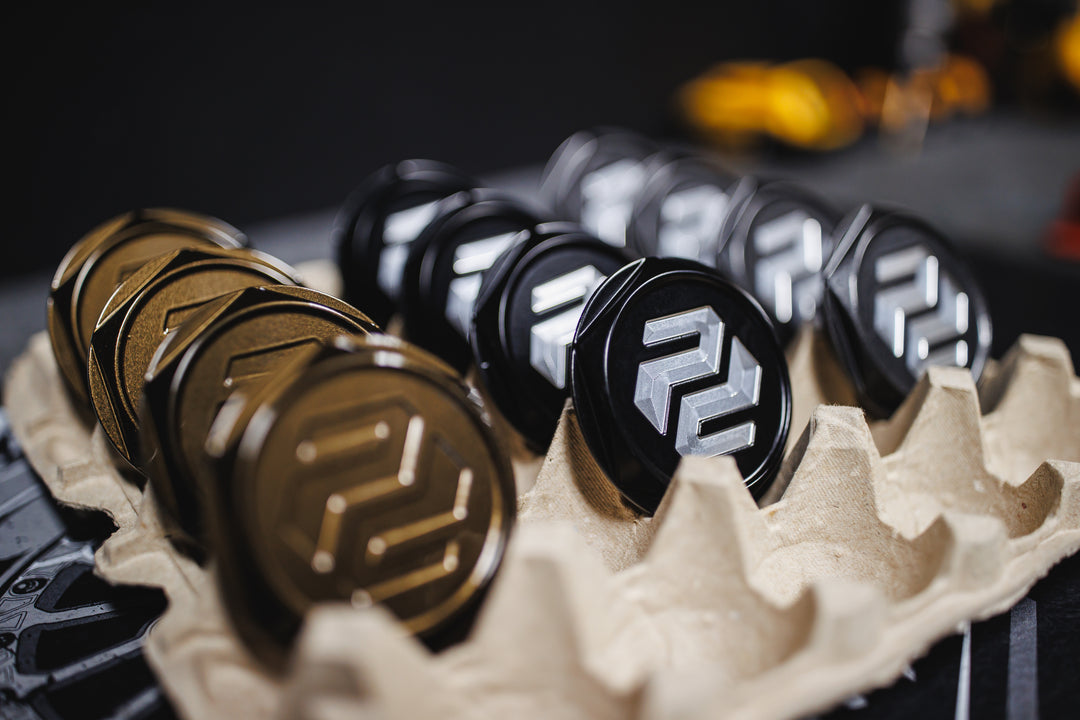
3. SPINNING
Metal spinning is the process used to produce Price Designs rims. It involves rotating circular sheets of forged American aluminum on a CNC lathe to form rims in many different diameters and profiles. During spinning, the aluminum is annealed by heating, and cooling at a controlled rate to increase strength, grain structure uniformity, and improve ductility. This enhances the ability to flex without breaking or cracking, un-like cast aluminum.
After spinning two wheel halves in specific sizes, profiles and diameters, they are then welded together to ensure a strong, tight seal for the life of the wheel.
4. FINISHING
Our finishing process typically involves powder coat, polishing, or post-cut operations. Powdercoat is the finishing process used to apply durable, decorative and protective coatings to our wheels. It involves applying dry powder with an electrostatic spray gun. The gun charges the powder particulates with an adjustable positive charge. The powder adheres to the grounded component and is then placed in an industrial oven for a heat cycle, typically at 350-400* for 30-45 minutes to achieve the finishes you see on Price Designs wheels.
Our in-house powder coat operation promotes our ability to be efficient, while constantly innovating and leading the industry in finish quality, and creativity. Often times we perform “post-cut” operations which involves placing powder coated parts back in the CNC mill to cut through the powder and reveal a machined, two-toned, custom finished component.
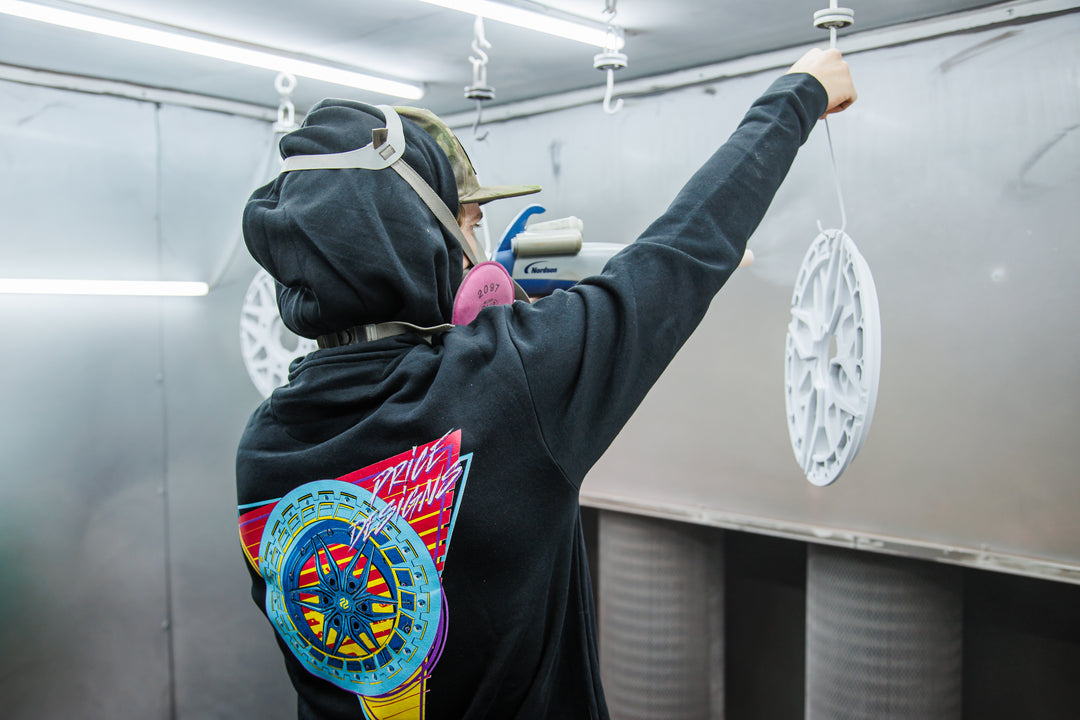
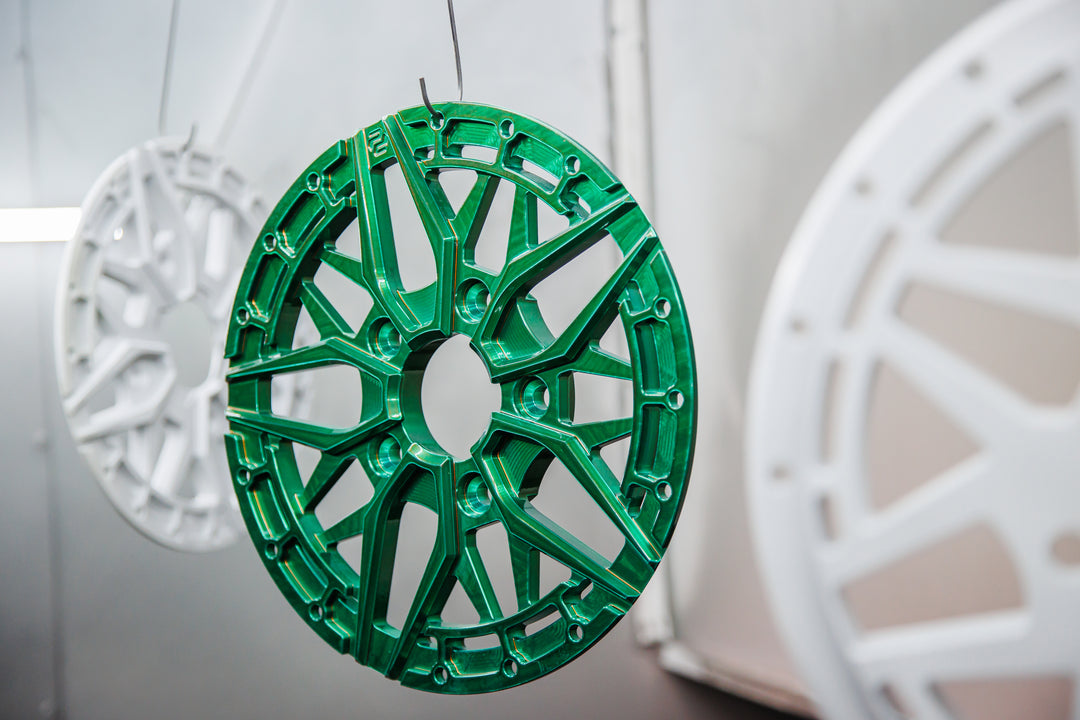
5. ASSEMBLY
The assembly process brings dreams to reality. After many hours of forging, spinning, machining, and finishing, it is finally time to assemble all components into a finished product. Our detail-oriented team hand assembles every wheel to ensure every part fits seamlessly, and inspects each component to control quality at every step of the way. Our efficient assembly process reduces production time without compromising quality. Each face bolt is hand-torqued to spec after applying threadlocker, to ensure tight fitment for the life of the wheel. We apply a simple ceramic quick coating in preparation for packaging.
Your wheels are complete.
We hope you enjoy the result as much as we enjoy the process.
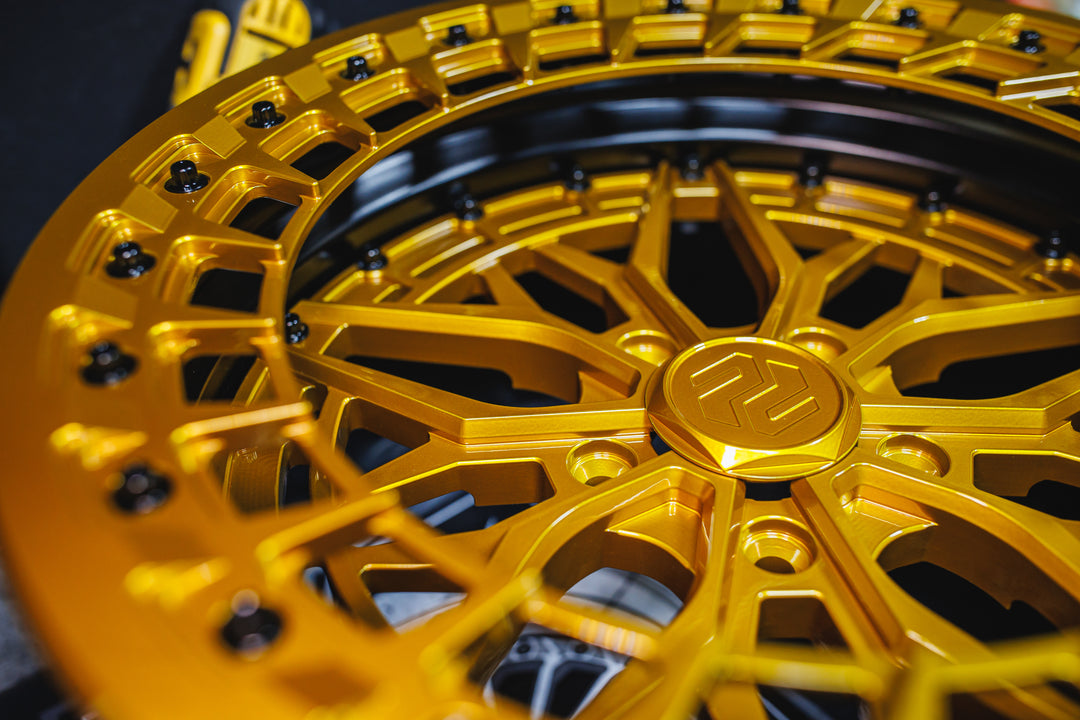
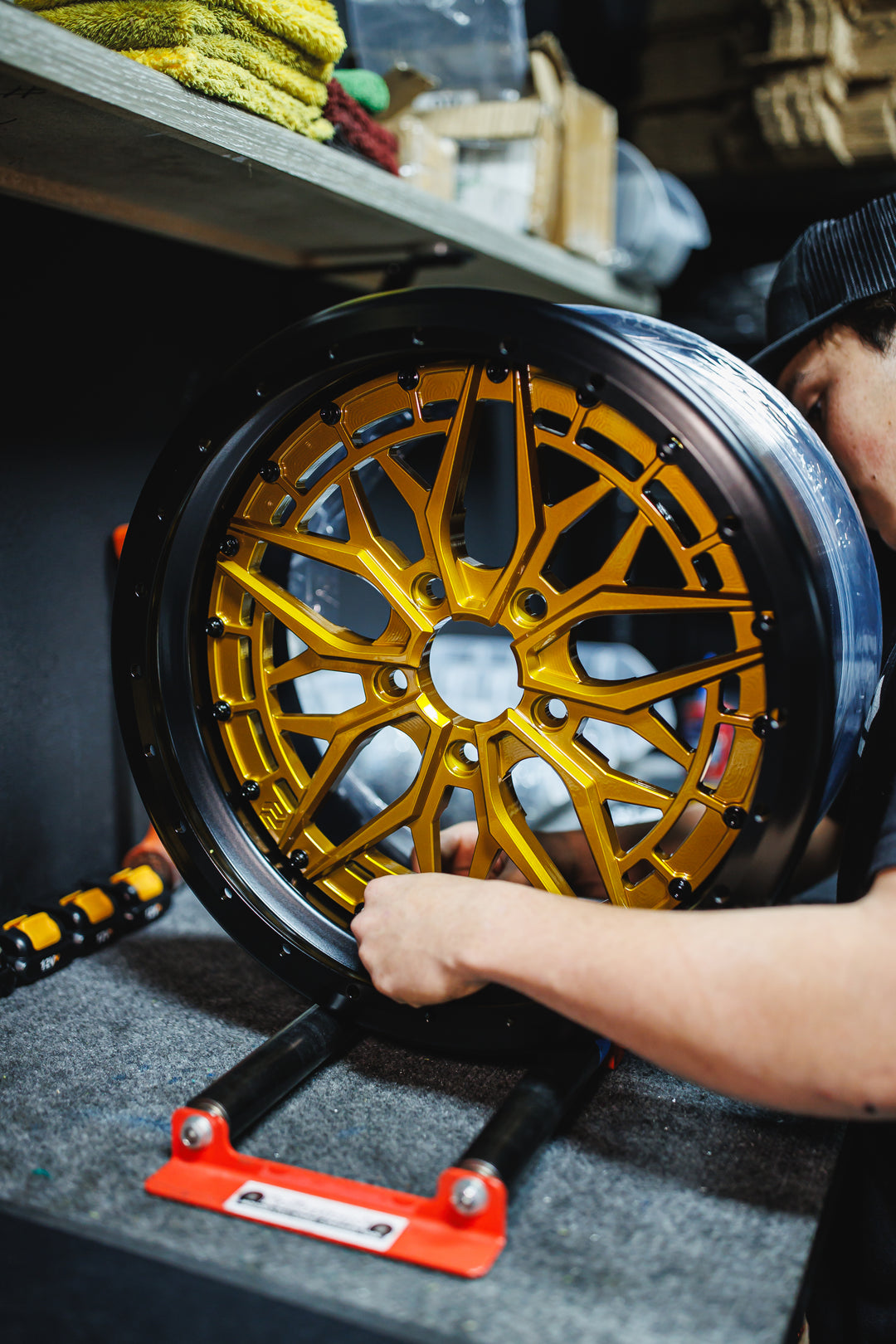
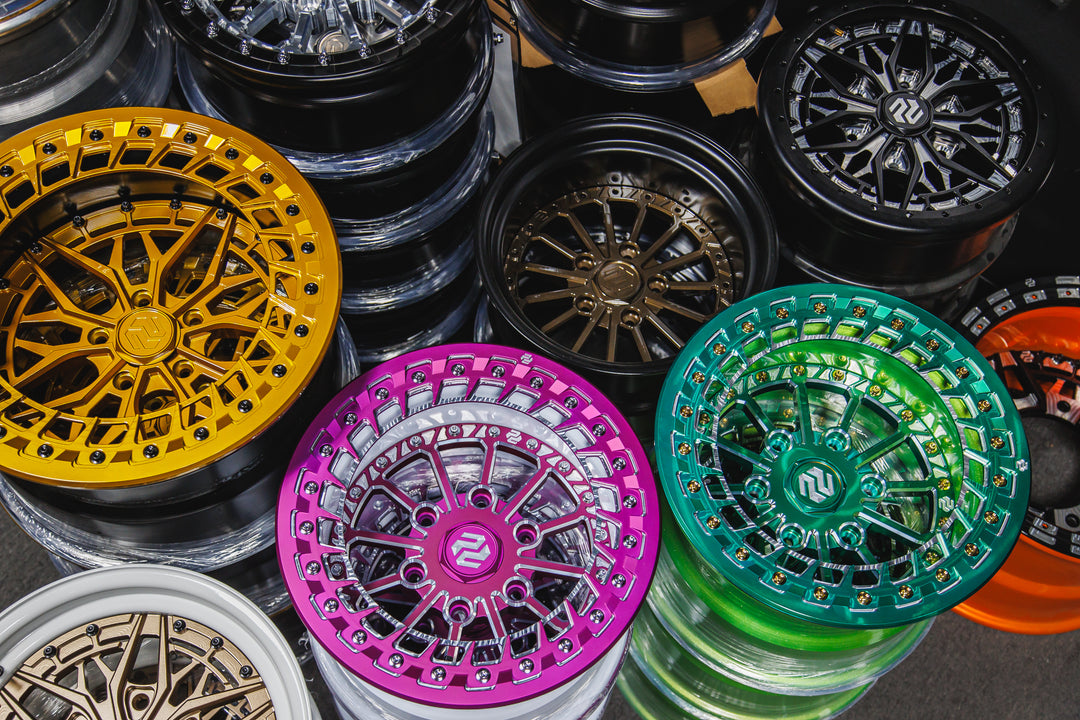